Is Your Aircraft in a High-Risk Corrosion Zone? Check the FAA Map.
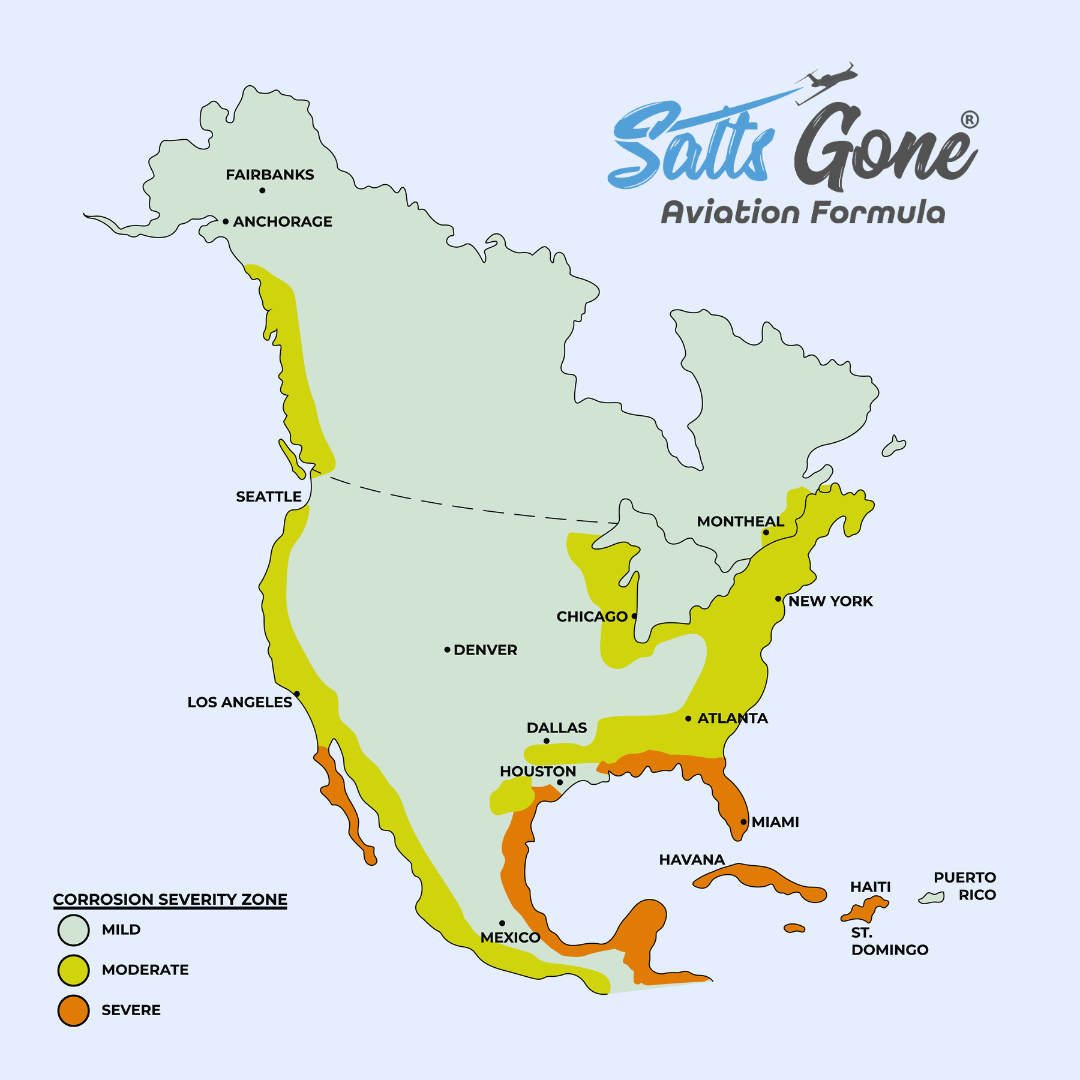
*Info from an Advisory Circular AC 43-4B via the FAA website*
For the FAA pdf click here.
Corrosion is one of the most underestimated dangers in aviation, silently compromising aircraft safety and performance. Whether you're flying in coastal areas or humid climates, corrosion can affect critical components, leading to costly repairs and potential hazards. Understanding where the risk is highest, as outlined by the FAA's corrosion map, is the first step in protecting your aircraft and ensuring its longevity. In this post, we’ll dive into the dangers of corrosion, how to identify it, and the best ways to prevent it before it impacts your aircraft.
Info from Section 1.6:
Background. Corrosion is the electrochemical deterioration of a metal because of its chemical reaction with a surrounding environment. While the aerospace industry is continuously developing new and better materials, progress is offset partly by a more aggressive operational environment and by the complexity of the corrosion phenomenon, which can take many different forms. The resistance of aircraft materials to corrosion can drastically change with only a small environmental change.
Info from Section 1.7 Catastrophic Corrosion Events:
Corrosion is most often a slow process of material deterioration, taking place over a long period of time. Examples are general corrosion, pitting, stress-corrosion cracking, environmental embrittlement, and corrosion fatigue and exfoliation. Corrosion degradation can occur very quickly, in days or even hours, and
with catastrophic results. Corrosion thrives on both the chemical and mechanical aspects of the environment and can cause catastrophic structural failure without warning.
1.8 Corrosion Control Program:
1.8.1: The possibility of an in-flight mishap or excessive down time for structural repairs mandates an active corrosion prevention and control program (CPCP). The operational environment of the aircraft sets the type and aggressiveness of the program. Aircraft exposed to such environments as salt air, heavy atmospheric industrial pollution, or over-water operations, will need a more stringent CPCP than an aircraft operating in a dry environment.
1.8.2:Operators must follow a constant cycle of cleaning, inspection, operational preservation, and lubrication to prevent corrosion. Prompt detection and removal of corrosion will limit the extent of damage to an aircraft and its components. The basic philosophy of a CPCP should consist of:
- Personnel adequately trained in recognizing corrosion, including conditions, detection and identification, cleaning, treating, and preservation;
- Thorough knowledge of corrosion identification techniques;
- Proper emphasis on the concept of all-hands responsibility for corrosion control;
- Scheduled corrosion inspections;
- Aircraft washing at regularly scheduled intervals;
- Routine cleaning or wipe down of all exposed unpainted surfaces;
- Keeping drain holes and passages open and functional;
- Scheduled inspections, removals, and reapplications of preservation compounds;
- Early detection and repair of damaged protective coatings;
- Periodic thorough cleaning, lubrication, and preservation;
- Prompt corrosion treatment after detection;
- Accurate record keeping and reporting of material or design deficiencies; and
- Use of appropriate materials, equipment, and technical publications.
For corrosion theory see the original post of the FAA pdf here. Scroll to page 2.1, Chapter 2.
For an in-depth look at corrosion based on metal types as well as problem points on an aircraft see Chapters 3 and 4 in the original document linked above.
Figure 4-15 on page 4-22 provides a map of corrosion with levels from mild, moderate, and severe. Not surprising, most of the U.S. falls into some state of corrosive environments.

Living in FL – Corrosion capital! Interested in info.
Leave a comment